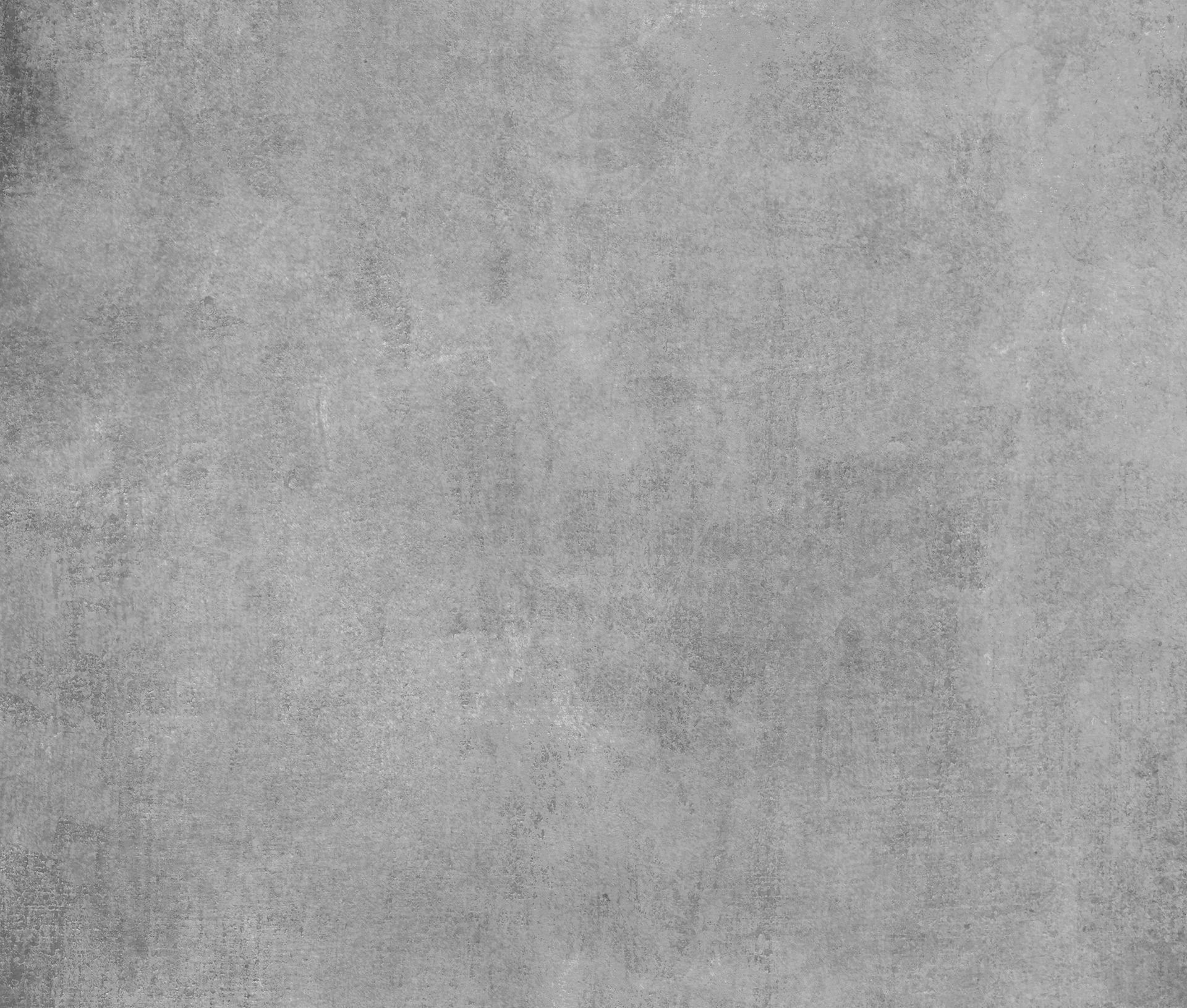

projects




Animatronic Brutus
I was project manager for the Theme Park Engineering Group as we designed our own animated figure: Brutus! The project timeline was a 6 week period. There were 4 main teams: Controls, Mechanical Design, Scenic Design, and SolidWorks Modeling.
​
Each team had a designated team lead that guided the group, taught important concepts regarding the team's goals, and made sure the team remained on schedule. I was in charge of the schedule, ordering materials, and communicating with each team lead for project updates and any major changes to the design. Each week, I would rotate about each of the teams to survey progress.
​
For the exterior of our figure, we decided to buy a stuffed animal Brutus and take out most of the stuffing. We then made important access points such as his back, arms, and legs. These access points were necessary to place our skeleton and servo motors into the body. We used 5 servo motors: 1 for his head tilt, 2 for his shoulders, and 2 for his elbows. As for our microcontroller, we programmed an Arduino. We were able to practice our soldering skills and teach incoming freshman how to use the soldering iron. For safety reasons and to limit the chances of wires shorting out, we used heat shrink to cover any solder points.
For scenery, we created a 3-fold poster that had 3 photos of significant locations on The Ohio State University campus. In addition to these photos, a clothes hanger was made into a mobile that hung above Brutus. This mobile had clay items attached representing different things about the school such as: a calculator, a buckeye nut, a block "O", and "Script Ohio".




Beast Car Model
I created this Beast car model in SolidWorks to gain experience working with the software. This project occurred before I received my certification for the software.
​
There are 5 unique parts to the assembly and the assembly is arranged in a way where the lap bars move appropriately.
​
I was inspired to create this model because the Beast attraction at Kings Island has always been one of my favorite roller coasters. I was never able to find any schematic of these cars so the dimensions and contour of each element is purely estimated from either memory or looking at photos. If you ever find yourself close to Cincinnati, Ohio, you should check out this unique attraction!
​
*Disclaimer: I do not own the rights to the Beast Trademark. This model was created as a personal project and was in no way used in correlation to the actual Beast attraction located at Kings Island in Mason, OH*
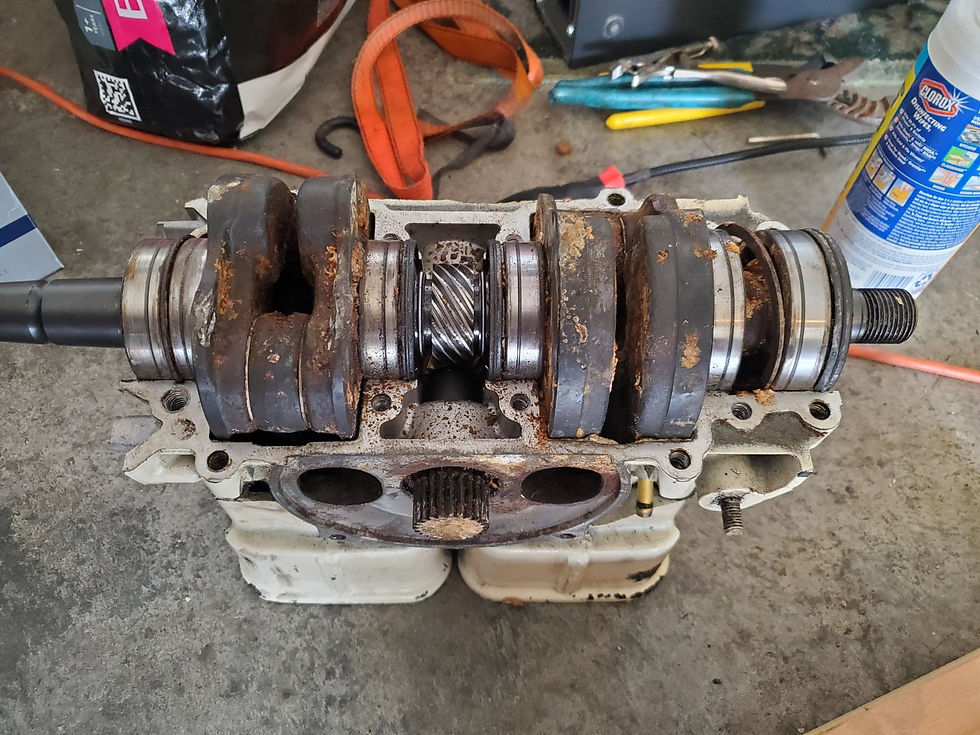
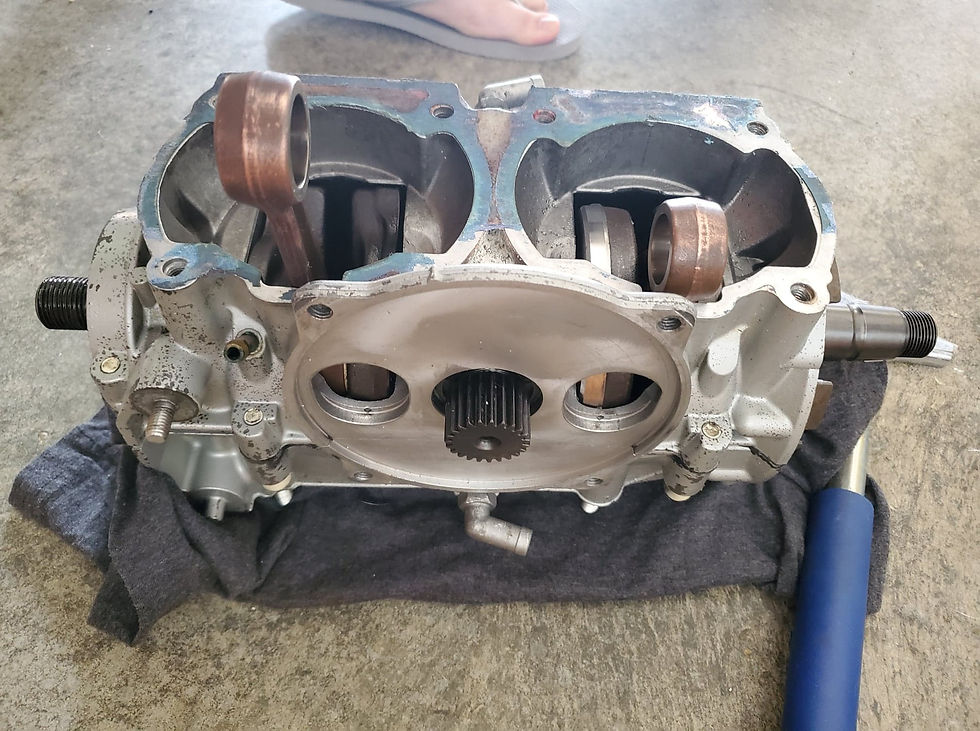
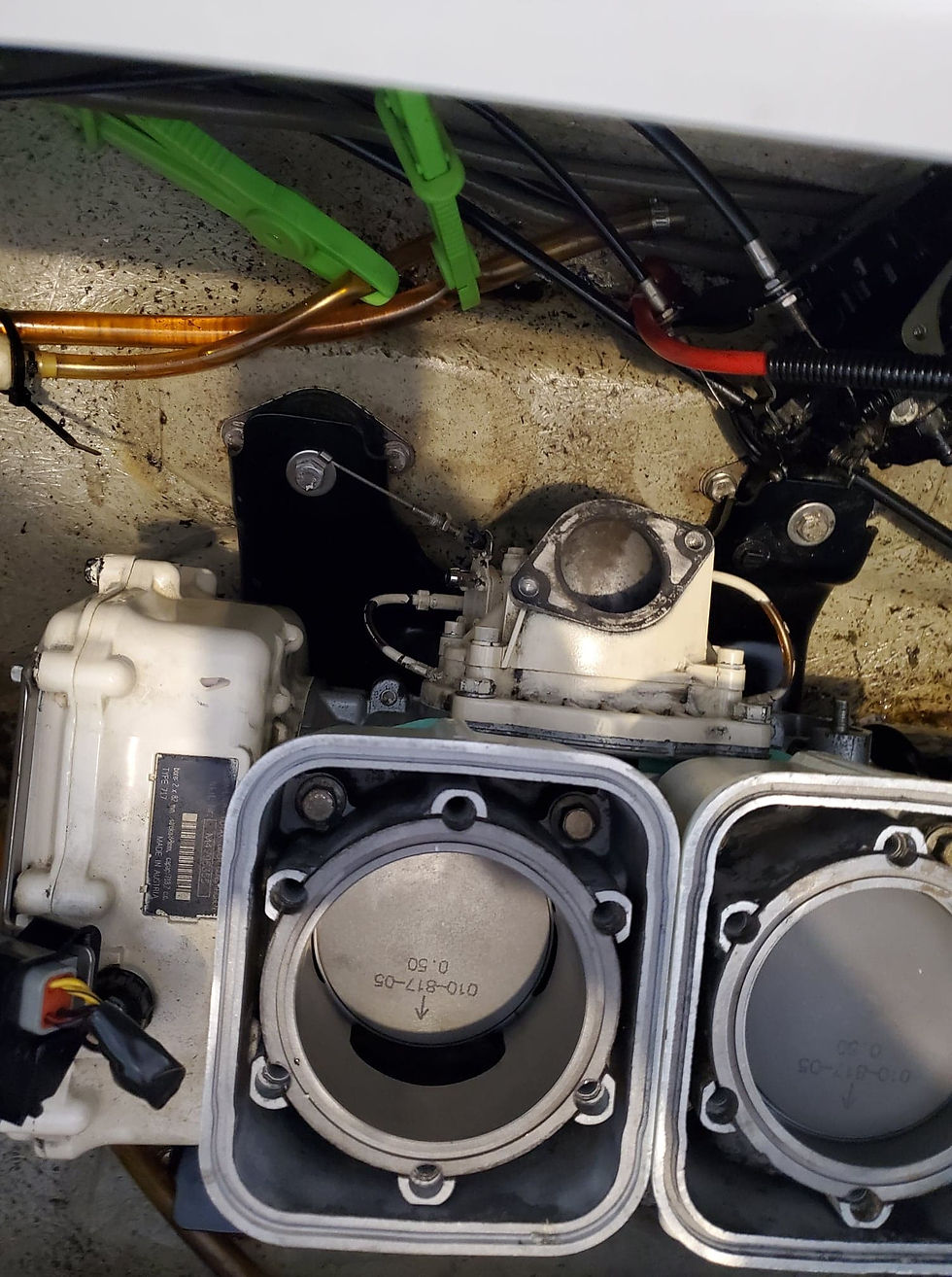
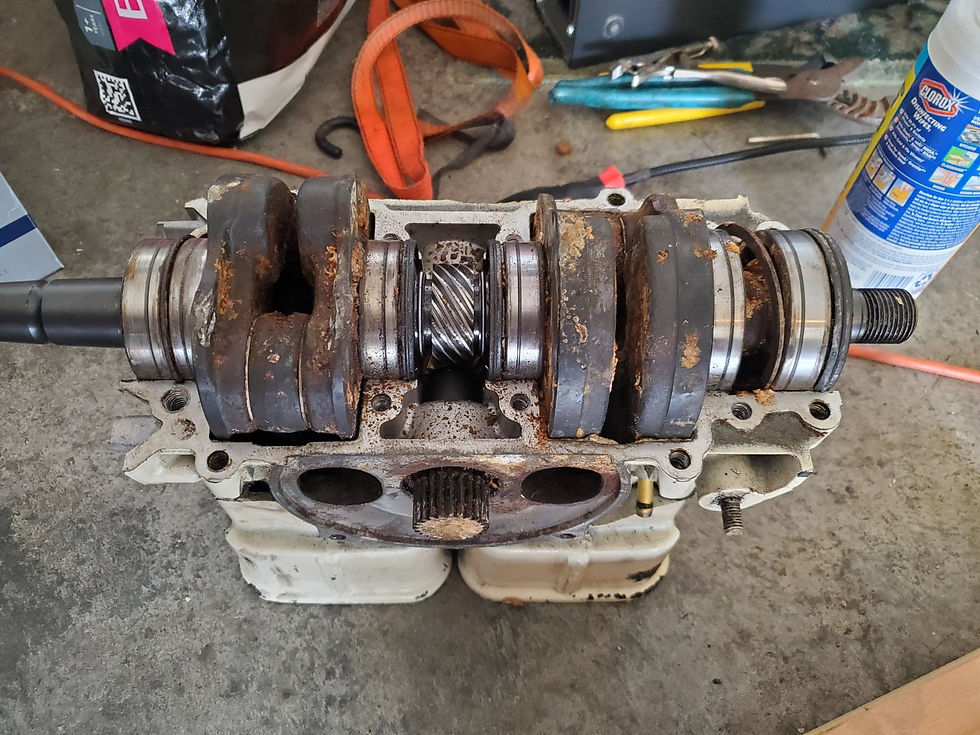
Jet Ski Engine
Replacement
Unfortunately, a bolt that fastened the base of the jet ski to the engine came loose and caused major vibrations. These vibrations caused serious damage to the engine. Additionally, the intake was damaged and allowed salt water to enter, further damaging the engine. Parts were ordered and I replaced the entire engine.
Imaginations Competition
The project was conceived by The Ohio State University's team and created for the 2019 Walt Disney's Imagineering Imaginations Design Competition. The project is the sole property of Walt Disney Imagineering and all rights to use these ideas are exclusive to Walt Disney Imagineering. The competition is a way for students and recent graduates to showcase their talents and for Walt Disney Imagineering to identify new talent.

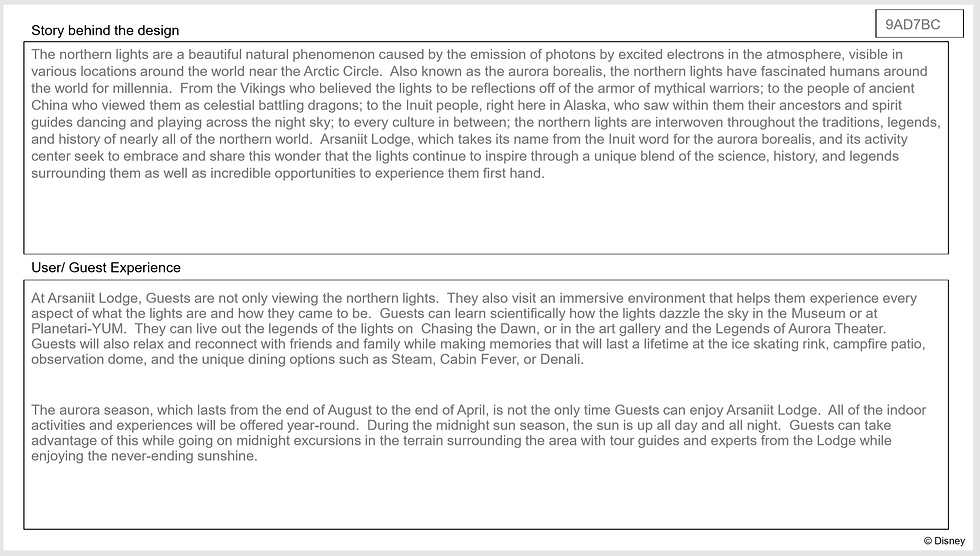


Make a Difference Project Pitch
I was one of the two project developers for this Theme Park Engineering Group project. As COVID-19 had a lot of effects upon the theme park industry, Kirsten Szydlowski and I wanted to plan a realistic event that could help. We partnered up with the Themed Entertainment Association Group at the University of Cincinnati and split into 3 major teams: Marketing, Operations, and Finance. We knew that there was a chance this event may never happen, but we wanted the experience of planning such a large event to understand what it requires. There were a number of mentors for this project, such as Tiffani DuScheid, who played a major role in reviewing our work and providing
great feedback.
​
As the semester progressed, we conducted a lot of research including a survey to the general public. This survey concluded with over 600 participants. Our idea for an event was to hold concerts in the large parking lots of Cedar Fair's Cedar Point and Kings Island. The guests would attend in their personal vehicles, safely spaced apart. This project required a lot of details. At the end of the semester, we presented our work to Cedar Fair for the opportunity to make it happen! If you are interested in learning more details about this project, please visit my contact page and
email me.


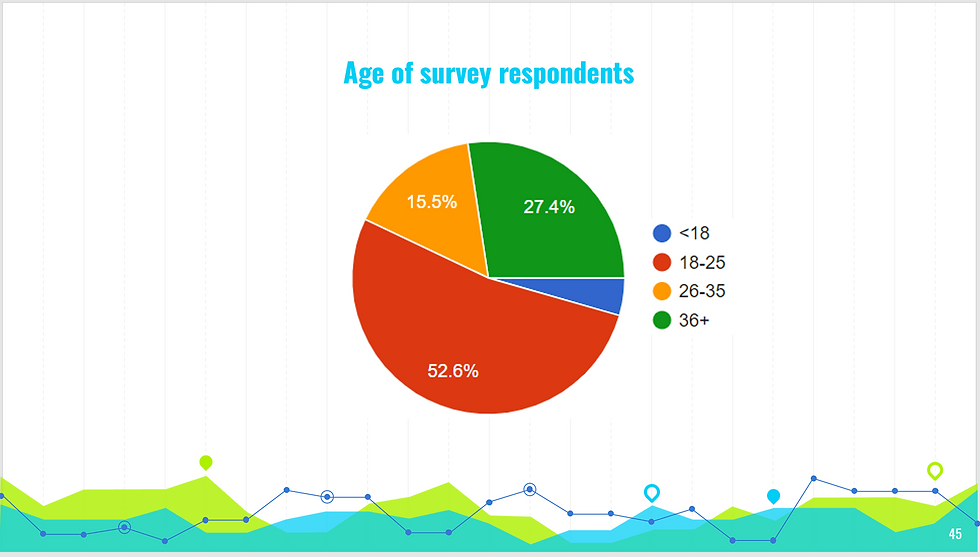

Senior Capstone,
Compact Joint Design: Prosthetic Hand
One of the main objectives of my senior capstone project was to implement the layer jamming technique into a prosthetic hand. The team designed the entire model, from the joint design to the actuation. Most of the model was 3D printed. The rigid palm and phalanges were printed with PLA and the flexible joints were printed with TPU. There is a small nylon cable that is pulled by a continuous servo motor to curl each individual finger. The layer jamming technique involves a number of thin Dura-Lar layers stacked within a latex wrap. There is a pump connected to these packages and when the negative pressure is activated, the layers are pushed together to stiffen the package. In this case, the packages are along the entire length of each finger, so when the pump is activated, the fingers will hold their current position.



